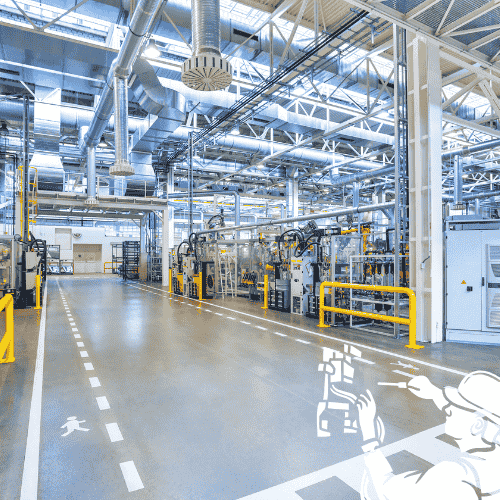
Industrial Electrical Services
Specialized solutions for manufacturing and industrial facilities
Industrial facilities demand electrical systems that deliver exceptional reliability, safety, and efficiency. From power distribution and machine wiring to automation controls and compliance requirements, industrial electrical infrastructure presents unique challenges that require specialized expertise.
At Teva Électrique, we understand the critical nature of electrical systems in industrial environments where downtime can result in significant production losses. Our team of industrial electrical specialists brings extensive experience in designing, installing, and maintaining robust electrical systems for manufacturing plants, processing facilities, and industrial operations of all sizes.
We work closely with facility managers, engineers, and maintenance teams to develop customized electrical solutions that enhance operational efficiency, ensure regulatory compliance, and maximize uptime. Our comprehensive industrial services encompass everything from new installations and system upgrades to troubleshooting, repairs, and preventive maintenance programs tailored to your specific industrial requirements.
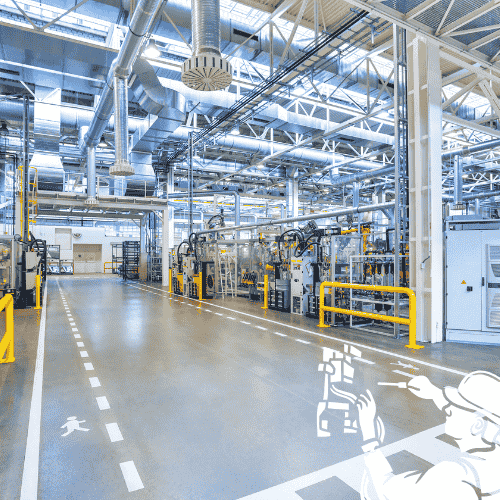
Expert Industrial Electrical Services Services
Our certified electricians ensure safe, code-compliant installations
Our Services
Power Distribution Systems
Design and installation of robust power distribution systems to efficiently deliver electricity throughout your industrial facility.
Machine & Equipment Wiring
Specialized wiring services for industrial machinery, equipment, and production lines to ensure optimal performance and safety.
Automation & Control Systems
Implementation of advanced automation and control systems to optimize your industrial processes and increase productivity.
Power Quality Solutions
Comprehensive power quality analysis and solutions to prevent equipment damage and production downtime.
Preventive Maintenance
Scheduled maintenance programs to identify potential issues before they cause costly downtime or safety hazards.
Safety Compliance & Inspections
Expert electrical safety inspections and upgrades to ensure compliance with industrial regulations and standards.
Why Choose Us
Experience the Teva Électrique difference for your residential electrical needs
Minimized Downtime
Our efficient project management and 24/7 emergency service help minimize costly production interruptions.
Safety Compliance
We ensure all industrial electrical work meets or exceeds relevant safety codes and standards.
Energy Efficiency
Our solutions optimize power consumption to reduce operational costs in high-demand industrial environments.
Experienced Technicians
Our team has specialized training and extensive experience in complex industrial electrical systems.
Frequently Asked Questions
How can we improve power reliability in our manufacturing facility?
Improving power reliability in manufacturing facilities requires a multi-faceted approach: 1) Implement a comprehensive power quality monitoring system to identify issues like voltage sags, harmonics, and transients that affect sensitive equipment, 2) Install appropriate surge protection devices at all levels of your electrical distribution system, 3) Consider power conditioning equipment such as voltage regulators, harmonic filters, or uninterruptible power supplies for critical processes, 4) Upgrade outdated distribution equipment including transformers, switchgear, and circuit breakers, 5) Establish a preventive maintenance program with regular thermographic scanning and testing of protection systems, and 6) Consider on-site power generation capabilities for critical operations. Our industrial power assessment can identify the specific vulnerabilities in your facility and recommend targeted solutions to maximize uptime.
What electrical considerations are important when installing new production equipment?
When installing new production equipment, several electrical considerations are critical: 1) Power requirements analysis to ensure your electrical system can handle the additional load without compromising existing operations, 2) Proper sizing of conductors, disconnects, and overcurrent protection devices based on equipment specifications and environmental factors, 3) Voltage drop calculations to ensure efficient operation, especially for equipment located far from distribution panels, 4) Harmonic mitigation for equipment with variable frequency drives or switching power supplies, 5) Integration with existing control systems and emergency stop circuits, 6) Proper grounding and bonding to prevent equipment damage and ensure personnel safety, and 7) Compliance with relevant industrial electrical codes and standards. We can coordinate with your equipment vendors to ensure proper installation while minimizing production disruptions.
How often should industrial electrical systems be maintained?
Industrial electrical systems require more frequent and thorough maintenance than commercial or residential systems due to their complexity and the consequences of failure. Critical components like transformers, switchgear, and motor control centers should be inspected quarterly, with comprehensive testing annually. Circuit breakers should undergo insulation resistance testing and contact resistance testing annually. Thermographic scanning should be performed semi-annually to identify hotspots before they cause failures. Motors and drives should have vibration analysis and insulation testing at least twice yearly. The specific maintenance schedule should be tailored to your facility's operating conditions, equipment criticality, and environmental factors. We can develop a customized preventive maintenance program that balances reliability requirements with maintenance costs.
Can you help us reduce energy consumption in our industrial facility?
Yes, we offer comprehensive industrial energy optimization services. Our approach includes: 1) Detailed power monitoring to establish baseline consumption patterns and identify major energy users, 2) Motor and drive system optimization, including replacement of standard efficiency motors with premium efficiency models and installation of variable frequency drives where appropriate, 3) Lighting system upgrades to LED technology with advanced controls, 4) Power factor correction to eliminate utility penalties and reduce distribution losses, 5) Compressed air system optimization to address one of the most inefficient utility systems in most facilities, 6) Heat recovery systems to capture and repurpose waste heat from industrial processes, and 7) Implementation of energy management systems to provide ongoing monitoring and control. Our industrial energy audits typically identify potential savings of 10-30% with reasonable payback periods.
What electrical safety measures should we implement in our industrial facility?
A comprehensive industrial electrical safety program should include: 1) Regular arc flash hazard analysis and labeling of equipment with appropriate warning labels and PPE requirements, 2) Implementation of lockout/tagout procedures with proper training and documentation, 3) Installation of appropriate safety interlocks on equipment and machinery, 4) Regular testing of ground fault protection systems and emergency power off systems, 5) Installation of adequate working space around electrical equipment as required by code, 6) Proper selection and maintenance of personal protective equipment for electrical work, 7) Regular safety training for both electrical and non-electrical personnel, and 8) Development of an electrical safety program that complies with NFPA 70E standards. We can help assess your current safety measures and implement improvements to protect both personnel and equipment while maintaining compliance with regulatory requirements.
Ready to Enhance Your Industrial Electrical Systems?
Contact us today to schedule a consultation and get a free quote for your industrial electrical project.
Get a Free Quote